Understanding Automotive Injection Molds: Revolutionizing Automotive Manufacturing
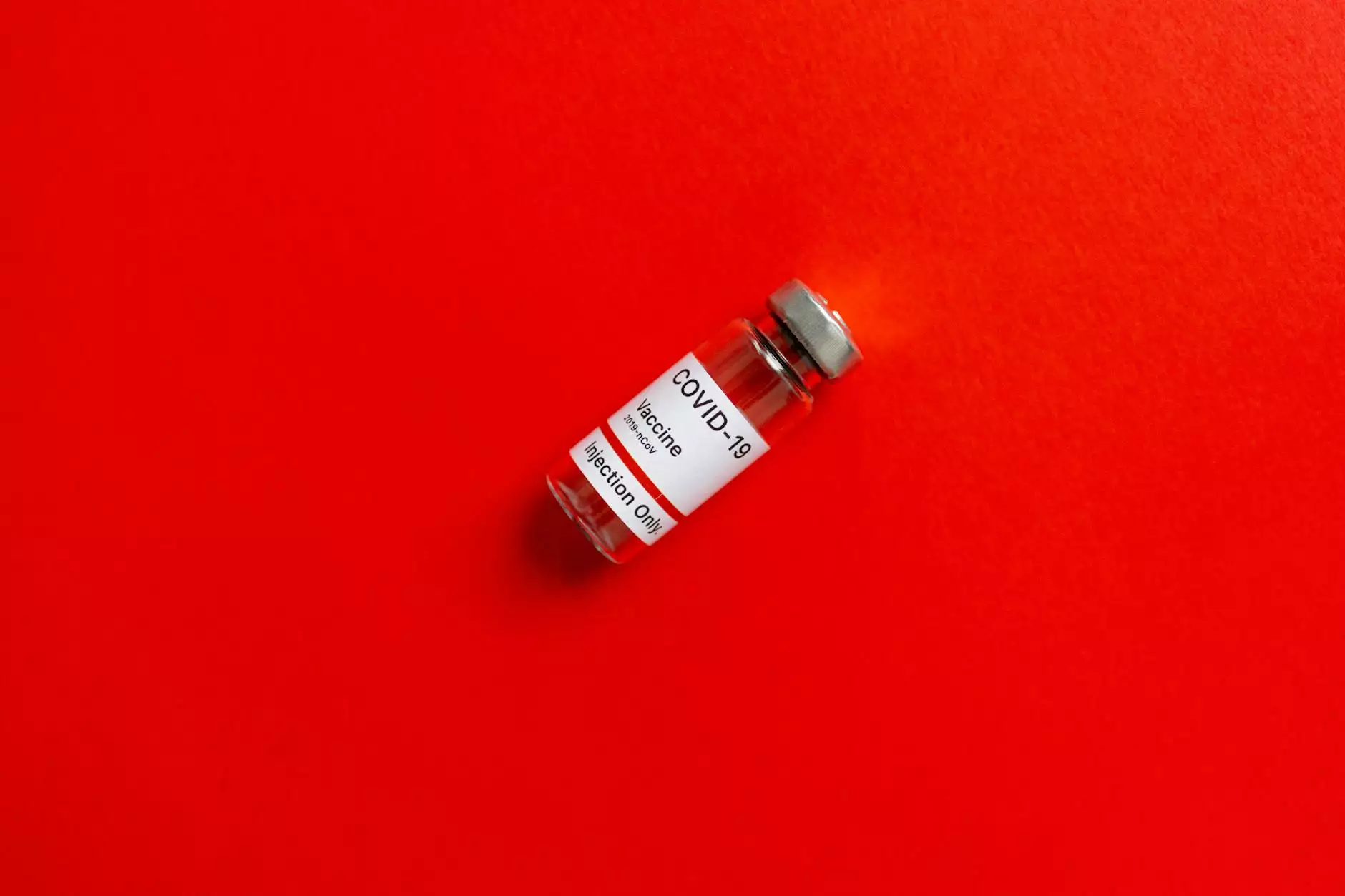
The automotive industry is a *dynamic* sector that continually evolves with technological advances. One of the cornerstones of this evolution is the automotive injection mold, which plays a pivotal role in the production of numerous components within vehicles. This article delves into the comprehensive aspects of automotive injection molding, covering everything from the basics to advanced applications, benefits, and future trends.
What is Automotive Injection Molding?
Automotive injection molding refers to the manufacturing process that involves injecting heated plastic into a mold to produce specific components for vehicles. This method is highly regarded for its ability to create complex shapes with precision and efficiency. The process generally involves:
- Designing the Mold: Utilizing CAD software to create a blueprint for the mold.
- Injection of Material: Heating plastic pellets until they melt and then injecting this material into the mold under high pressure.
- Cooling: Allowing the material to cool and solidify in the mold’s shape.
- Extraction: Removing the finalized part from the mold and performing any post-processing if required.
This process allows manufacturers to produce a wide array of plastic components, from *dashboard panels* to intricate *safety features*, with high precision and reduced production times.
Advantages of Using Automotive Injection Molding
Automotive injection molding provides several benefits that contribute to its popularity among manufacturers. Here are some of the key advantages:
- Cost Efficiency: Once the initial mold is created, producing individual parts becomes relatively inexpensive, especially in high volume.
- High Precision: The process allows for tight tolerances, producing parts that fit together seamlessly.
- Versatility: A wide variety of materials can be used, including thermoplastics and thermosetting plastics, catering to different needs in the automotive sector.
- Complex Geometries: Injection molding can create intricate shapes that might be difficult or impossible to achieve using other manufacturing methods.
- Reduced Waste: The process minimizes material waste compared to traditional manufacturing techniques.
Key Materials Used in Automotive Injection Molding
The selection of materials is crucial to the success of automotive manufacturing. Here’s a look at commonly used materials in automotive injection molding:
- Polycarbonate (PC): Known for its impact resistance and good clarity, making it ideal for headlights and clear covers.
- Polypropylene (PP): Flexible and chemical resistant, used in interior parts and exterior panels.
- ABS (Acrylonitrile Butadiene Styrene): This material combines toughness and rigidity, commonly found in bumpers and dashboards.
- Nylon (PA): Excellent for durability and heat resistance, often used in engine housings and electrical components.
Selecting the right material is essential, considering factors such as strength, weight, and cost implications in production.
Applications of Automotive Injection Molds
The application of automotive injection molds is vast, covering various components and systems within a vehicle:
1. Interior Components
Interior parts, such as *console trays*, *door panels*, and *dashboard elements*, are produced using injection molding to ensure both aesthetic appeal and durability.
2. Exterior Components
From *bumpers* to *grilles*, exterior parts must withstand harsh environmental conditions. Injection molding provides a way to create resilient outer components that maintain their shape and protect crucial systems.
3. Safety Components
Injection molding is pivotal for producing safety features like *airbag housings* and *seatbelt components*. The high precision required in these components ensures they perform their functions effectively during emergencies.
4. Functional Components
Many functional components, such as *ducting and ventilation parts*, rely heavily on injection molding. The ability to create complex designs makes this suitable for optimizing airflow within vehicles.
The Process of Automotive Injection Molding
Understanding the complete process gives insight into how injection molds are created and utilized:
The Design Phase
The design of an injection mold is a crucial step. Engineers collaborate with designers to create a mold that accommodates the specific part’s geometry, ensuring effective material flow, cooling, and quick ejection.
Mold Fabrication
Once the design is approved, the mold is fabricated using CNC machines or EDM (Electro Discharge Machining). Materials used for molds include steel or aluminum, selected based on production volume and cost considerations.
Testing and Validation
before mass production, a series of tests and validations are executed. This phase identifies any design flaws or potential production issues, which can be rectified before full-scale manufacturing begins.
Mass Production
After successful validation, the production process commences, leveraging the efficiency of automated machines to produce parts at scale while maintaining quality standards.
Future Trends in Automotive Injection Molding
The automotive industry is moving towards greener and more efficient practices, and injection molding is no exception. Here are some future trends:
- Innovative Materials: The development of new bio-based plastics and reinforced composites is changing the landscape of automotive manufacturing.
- Smart Manufacturing: Incorporating IoT and automation in the injection molding process leads to increased efficiency and reduced downtime.
- Sustainability: The focus on reducing carbon footprints is prompting manufacturers to reconsider their material choices and recycling options within the injection process.
Conclusion
In conclusion, automotive injection molding stands as a critical element in the automotive manufacturing process. Its ability to produce high-quality, precise components rapidly makes it indispensable in today's competitive automotive landscape. As the industry moves forward, the techniques and technologies surrounding injection molding are expected to evolve further, cementing its place as a cornerstone of automotive production. For businesses looking to enhance their manufacturing processes, investing in advanced automotive injection molds by experts in the field, such as those at DeepMould.net, is a step towards achieving operational excellence.